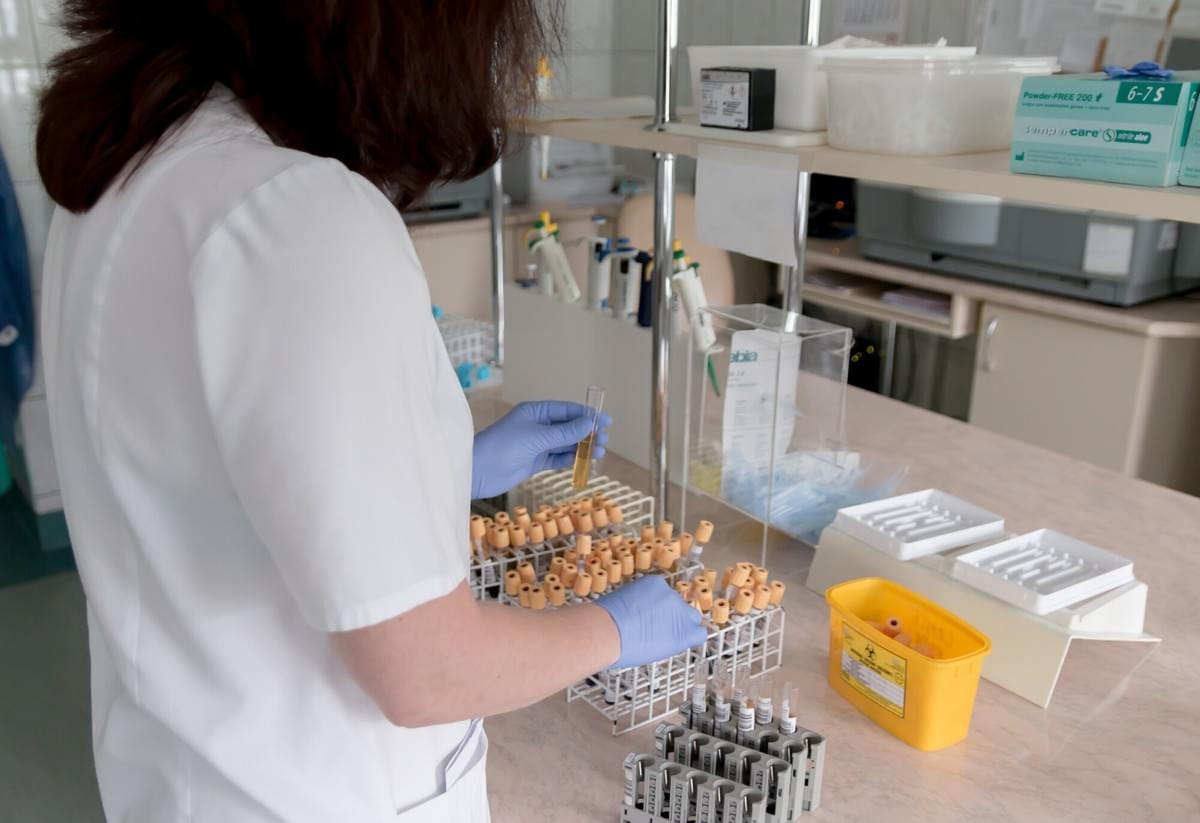
Equipment failure can be a costly and frustrating experience for any organization. From production lines to critical infrastructure, equipment failure can have significant consequences on both the bottom line and operational efficiency. That's why failure analysis is a crucial process in identifying the root cause of equipment failure and implementing corrective measures to prevent future failures. In this article, we'll delve into the world of failure analysis labs, exploring the importance of these facilities in modern industry and the benefits they bring to organizations.
1. What is a Failure Analysis Lab?
A failure analysis lab is a specialized facility designed to investigate and analyze equipment failures. These labs are equipped with advanced equipment and technologically advanced tools to examine components, materials, and systems to determine the root cause of failure. The primary objective of a failure analysis lab is to identify the root cause of equipment failure and provide recommendations for corrective action to prevent future failures.
2. Importance of Failure Analysis
Failure analysis is a crucial process in equipment maintenance and reliability engineering. It allows organizations to identify and correct design, material, or manufacturing flaws that can lead to equipment failure. By analyzing failed components, failure analysis labs can help identify the root cause of failure, which can then be used to implement corrective actions to prevent future failures.
3. Benefits of Failure Analysis
Failure analysis offers numerous benefits to organizations. By identifying the root cause of equipment failure, organizations can implement corrective actions to prevent future failures. This, in turn, can reduce downtime, increase operational efficiency, and reduce maintenance costs. In addition, failure analysis can help organizations improve the overall design and performance of equipment and systems, leading to improved productivity and reduced manufacturing costs.
4. What is Investigated in a Failure Analysis Lab?
Failure analysis labs investigate a wide range of equipment failures, including mechanical, electrical, and electromechanical systems. These labs examine components, materials, and systems to identify the root cause of failure. Investigations may include non-destructive testing, materials testing, and chemical analysis to determine the composition and properties of materials.
5. Techniques Used in Failure Analysis
Failure analysis labs employ various techniques to investigate equipment failures. These techniques include:
• Visual inspection: A detailed examination of the failed component to identify any visible signs of failure.
• Non-destructive testing: Techniques such as radiography, ultrasound, and magnetic particle testing are used to examine the internal structure of components without damaging them.
• Materials testing: Samples of materials are analyzed to determine their composition, properties, and failure mechanisms.
• Chemical analysis: Chemical testing is used to determine the presence of contaminants, corrosion, or other factors that may have contributed to equipment failure.
6. Importance of Documentation in Failure Analysis
Documentation is a crucial aspect of failure analysis. Detailed documentation of the investigation, including photographs, measurements, and test results, is essential for accurate diagnosis and corrective action. Documenting the investigation helps ensure that all relevant information is captured and allows for effective communication with stakeholders, including manufacturers, suppliers, and clients.
7. Effective Failure Analysis Methods
Effective failure analysis is critical to uncovering the root cause of equipment failure and implementing corrective actions. The following steps are essential for effective failure analysis:
• Clearly define the problem: Identify the equipment failure and its impact on operations.
• Gather data: Collect relevant information, including operational data, maintenance records, and witness statements.
• Conduct an investigation: Utilize various techniques, such as non-destructive testing, materials testing, and chemical analysis to investigate the failure.
• Analyze the data: Interpret the test results and data collected during the investigation.
• Identify the root cause: Determine the underlying cause of equipment failure.
• Implement corrective actions: Based on the findings, develop and implement corrective actions to prevent future failures.
8. The Role of Failure Analysis in Industry
Failure analysis is a critical process in various industries, including manufacturing, aerospace, energy, and healthcare. In these industries, equipment failure can have significant consequences, including:
• Downtime and lost productivity
• Increased maintenance costs
• Risk to human life and safety
• Environmental damage
9. Conclusion
Failure analysis is a vital process in ensuring the reliability and performance of equipment and systems. By understanding the root cause of equipment failure, organizations can implement corrective actions to prevent future failures, reducing downtime, maintenance costs, and improving overall operational efficiency.